This Quality Management Plan outlines the roles and responsibilities of the team members involved in the Hydraulic Fracturing Study. It provides a framework for ensuring that all relevant information is collected, analysed and used effectively.
This plan is an integral part of the overall project and its successful implementation is essential for the timely and successful completion of the project.
Overview of Quality Management Plan
A Quality Management Plan (QMP) is an important document that outlines the management systems and processes of an organization to ensure the delivery of high-quality goods and services. It defines a framework of quality assurance, control, and continual improvement within the scope of an organization.
The main purpose of a QMP is to ensure that all personnel involved in a project know exactly what quality management strategies need to be implemented for it to be successful. This plans also serves as a reference document on how to monitor and review performance metrics related to project goals.
The QMP should include, at minimum: roles & responsibilities, quality objectives, quality standards, inspection and test plans (ITPs), critical suppliers/contractors information, and corrective/preventive actions. The plan should clearly define who is responsible for each activity related to the project’s quality planning process and ensure timelines are adhered too.
Additionally, each task should be clearly defined so that all stakeholders understand their roles to carry out these tasks effectively and efficiently while always staying within budget constraints.
Roles and Responsibilities
When putting together a Quality Management Plan, it is important to consider one of the most integral elements, roles and responsibilities. By detailing the roles and responsibilities involved in quality management, you can ensure you have the right people and resources to enact the plan.
This article will examine the roles and responsibilities in a Quality Management Plan for the Hydraulic Fracturing Study.
Project Manager
The Project Manager is responsible for the overall direction, coordination, implementation, execution, control and completion of the project. The Project Manager shall determine and find appropriate solutions to identified problems to ensure timely and successful completion.
The Project Manager is accountable to the Sponsor/Steering Committee or other suitable governance bodies for successful completion of the project. Responsibilities include:
-Leading project planning activities including creating schedules, project plans and risk plans.
-Organizing budgets and resources.
-Identifying risks and taking action to prevent them from occurring.
-Monitoring progress within the team against agreed targets.
-Auditing quality assurance processes in line with established guidelines which typically includes recommendations for improvement or corrective action when required
-Ensuring that communication channels are open with all stakeholders continuously throughout the project
-Capturing issues that arise during a project lifecycle and make recommendations for resolution.
Quality Assurance Manager
The Quality Assurance (QA) Manager is responsible for ensuring the most up-to-date quality standards and practices are being followed. The QA Manager ensures that all products and services the organization produces meet established quality standards. This requires active involvement in planning, managing, and evaluating the quality assurance program, as well as its components including audits, inspections, reviews and corrective action plans.
The primary responsibilities of a QA Manager include:
- Create appropriate documentation systems such as procedures manuals, checklists, templates and quality control plans in coordination with other departments
- Develop a system to monitor customer complaints and feedback
- Conduct internal audits to identify areas of improvement or noncompliance with
- standards or regulations
- Develop strategies for eliminating quality difficulties
- Analyze findings from monitoring activities to inform decisions about process or product improvements
- Prepare reports for various stakeholders on quality issues or progress
- Review safety procedures and policies periodically to ensure that they are up to date
- Address customer service concerns promptly
Quality Control Manager
The Quality Control Manager is responsible for developing, implementing and monitoring the Quality Management Plan to ensure that the final product meets customer requirements. The role of the Quality Control Manager involves:
-Developing and maintaining a quality system, which includes defining processes, procedures, forms and instructions.
-Ensuring all personnel have appropriate training on quality procedures, products etc. as well as any applicable regulations or standards.
-Conducting internal audits to verify compliance and effectiveness of processes.
-Monitoring process results to identify areas for improvement.
-Managing corrective and preventive actions from assessments including customer complaints.
-Analyzing data from production systems to identify trends related to product quality.
-Managing interactions with third party inspection bodies providing evaluations or certifications for materials or products.
-Participating in continual improvement initiatives including planning, implementation and review.
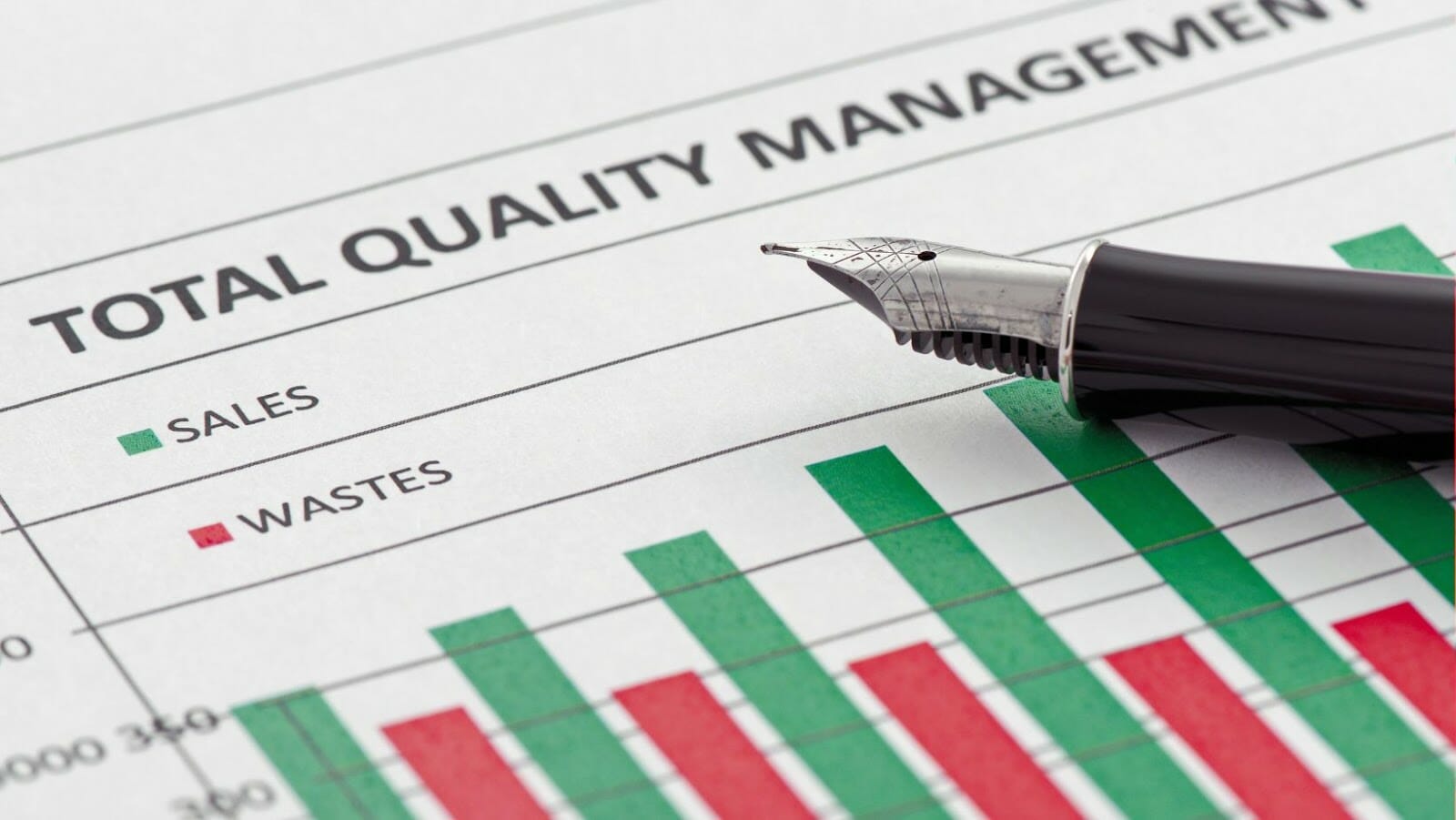
Laboratory Manager
The laboratory manager is a key member of the Quality Management Plan team and is responsible for meeting the reliability standards of the finished product. The following are the main tasks and responsibilities of the laboratory manager:
• Supervise all laboratory staff, including selection and training for their positions;
• Establish procedures and protocols for performing tests and collecting data;
• Monitor to ensure laboratories comply with all government regulations and requirements;
• Perform statistical quality assurance programs on raw materials, in-process materials and finished products;
• Maintain high safety standards in the laboratory environment;
• Monitor new technologies to improve test accuracy, repeatability, cost savings and manual processes;
• Analyze results from regular inspections or performance reviews to identify areas for improvement to enhance quality assurance systems.
Technical Personnel
Technical personnel perform functions such as producing and maintaining quality management system documents, carrying out audits, investigating customer complaints, and providing technical support. They are also responsible for training personnel in quality-related activities and ensuring that detailed requirements have been correctly understood and implemented.
Technical personnel includes quality engineers (QEs) who provide technical expertise for problem resolution, process/product/service improvement, team activities, customer satisfaction issues and other activities related to improving product/service quality. They are also responsible for developing processes related to cost control and process management. These processes include inspecting incoming materials, performing sampling operations, monitoring production processes and conducting verification/validation tests. A QE should ensure that all internal controls are properly established and maintained to meet the organization’s specified goals for quality.
Quality control (QC) personnel use statistical methods to check product or service performance against established standards in terms of reliability and effectiveness before it reaches customers or the market. Quality control staff should know project management concepts such as statistical process control techniques; know how to conduct software testing; understand root cause analysis; have a clear grasp of managing nonconforming materials; must possess auditing techniques in deliberation of procedures applicable during manufacturing cycle with supplier qualification/evaluation capabilities; possess analytic skills coupled with observations capability relative to hazardous substance issues identification or abatement protocols implementation; a working knowledge in problem-solving methods using Six Sigma principles is highly beneficial; strong organizational skills including database operation knowledge is important when necessary digital storage options must be employed along with communication skills relative to implementation of up-to-date administrative reporting systems pertinent to incident investigations resolution.
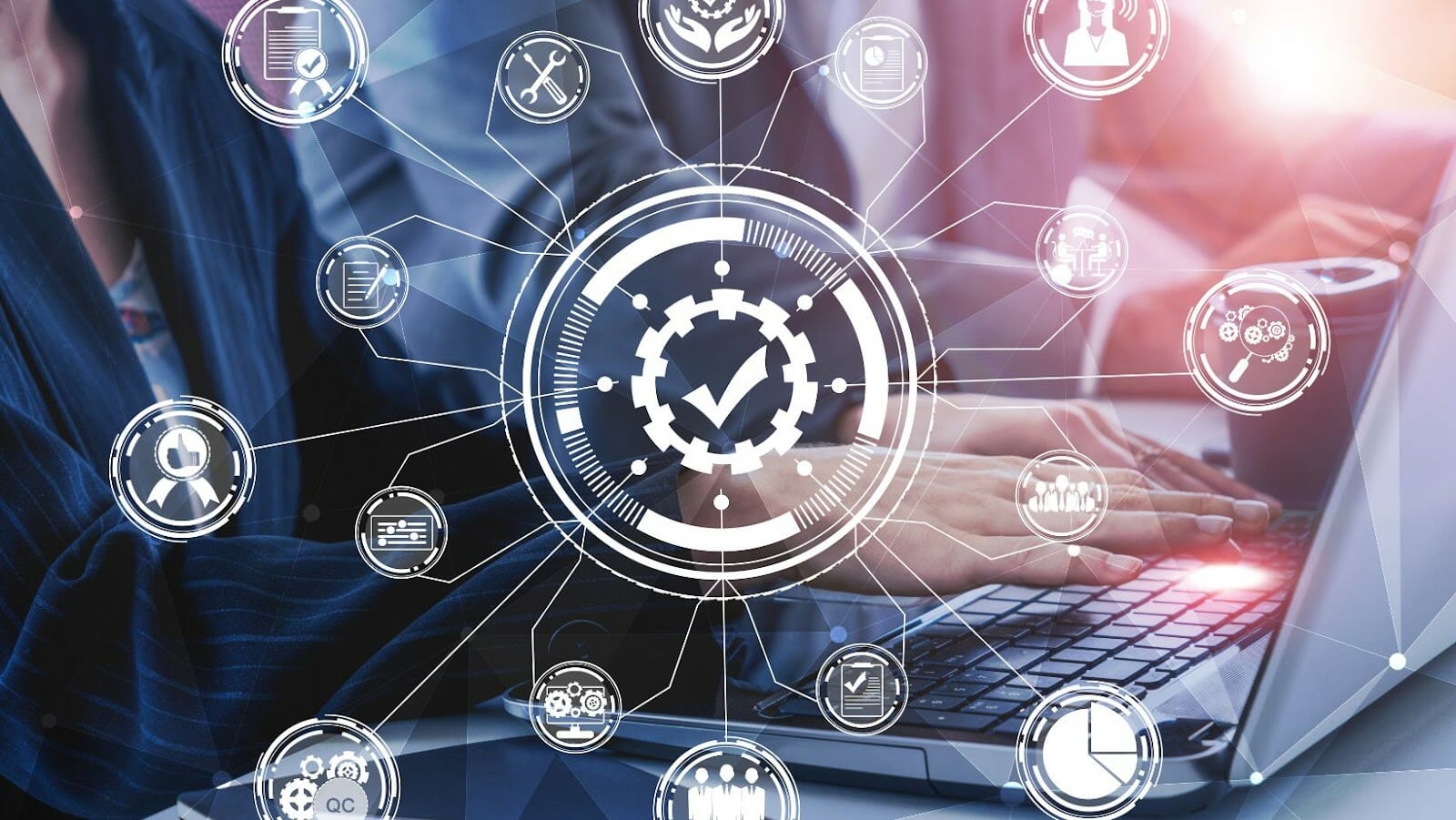
Quality Assurance and Quality Control
Quality Assurance (QA) and Quality Control (QC) are essential components of a Quality Management Plan for the Hydraulic Fracturing Study. QA focuses on the process of producing the output and making sure that processes are followed, while QC focuses on the results.
This article will explain the roles and responsibilities of both QA and QC about the Hydraulic Fracturing Study.
Conclusion
The Quality Management Plan is a critical document for ensuring the quality of an organization’s products and services. It provides a permanent record of the roles and responsibilities of those involved in maintaining and improving the quality of those products or services. The QMP should always be reviewed, updated and fine-tuned as the organization changes, grows and responds to customer feedback or external factors that affect the quality of their offering.
At pany XYZ, our Quality Management Plan has been implemented to ensure we consistently provide our customers with high-quality products. The plan outlines clear roles and responsibilities for each person involved in the product development process and creates a system of accountability through measurement, inspection, testing and continuous improvement plans.
By putting this plan in place at pany XYZ, we are taking steps towards not only developing better-quality products but also creating efficiencies throughout our whole production process from start to finish. This ultimately leads to improved customer satisfaction leading to more repeat business for our organization – something that is vitally important for long-term success in any competitive industry.
tags = Quality Management Plan, Hydraulic Fracturing Study QMP, Analysis of Existing Data, qa institute jeff allen facebookedelmanwired, qa integrity jeff facebookedelmanwired